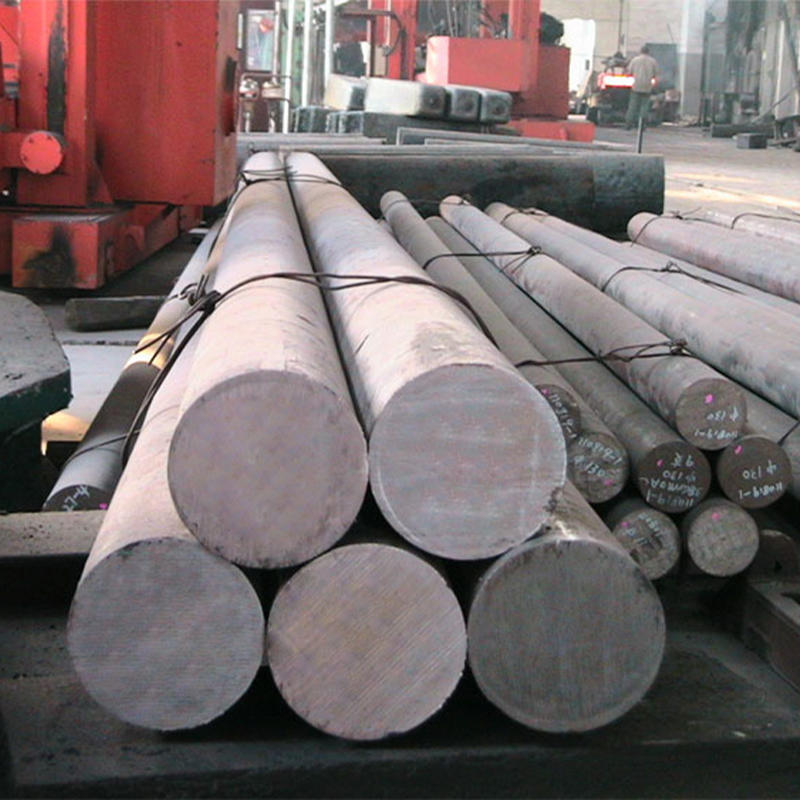
The forging process is a mechanical procedure that involves shaping a metal using compressive forces, which leads to a significant improvement in the internal structure of the material. Unlike cast alloys, which may contain internal voids or porosity, forged alloy round bars achieve a fine-grain structure where the metal's molecules are tightly aligned and evenly distributed. This results in a much denser and more homogeneous material. The consistent grain flow created during forging contributes to better overall mechanical properties, including greater fatigue resistance. The lack of internal defects makes the forged alloy round bars more capable of withstanding dynamic and cyclic loads without initiating cracks, significantly improving their longevity and reliability in mechanical applications subjected to repeated stress.
Fatigue strength refers to the material's ability to resist failure due to repeated or fluctuating stress over time. Forged alloy round bars offer superior fatigue resistance when compared to other materials like cast or rolled bars. The reason for this is that the forging process minimizes potential weak points that could lead to crack initiation. The elimination of internal defects such as air pockets or inclusions that are common in cast products results in a more reliable material that can endure repetitive loading cycles without experiencing failure. In industries like automotive, aerospace, and heavy machinery, where parts are frequently subjected to cyclic stresses, this high fatigue strength is critical for ensuring the part's longevity and performance over time.
One of the inherent benefits of forging is the densification of the material. During the forging process, the metal is compressed, which removes any internal air pockets and ensures that the material becomes denser than cast or wrought materials. The increased density of forged alloy round bars improves their ability to resist fatigue because denser materials are less prone to the development of microcracks, which can grow under repeated stress. A uniform, dense structure allows the bar to distribute applied loads more evenly, reducing localized stress points that could otherwise lead to cracks or premature failure. This improved density contributes directly to the durability and performance of forged alloy round bars in high-stress applications, such as in rotating machinery, turbine blades, or structural components.
Stress concentrations occur when the material experiences high localized stress at specific points, such as sharp edges, holes, or other geometric discontinuities. Forged alloy round bars are less susceptible to stress concentrations due to the way the material is shaped and formed during forging. The forging process ensures that the grain flow aligns with the shape of the part, effectively reducing the likelihood of stress concentrations that could lead to crack initiation. In comparison, materials that are cast or welded may have grain structures that are less uniform, which can lead to weak spots. By minimizing stress concentrations, forged alloy round bars exhibit higher resistance to crack formation under dynamic loading, which contributes to their enhanced fatigue resistance and prolonged service life.
Toughness refers to a material's ability to absorb energy before fracturing, which is especially important in applications where components are subject to sudden impacts, shocks, or vibrations. The forging process imparts greater toughness to forged alloy round bars by enhancing the material's microstructure, making it more capable of absorbing energy without cracking. The combination of improved toughness and enhanced fatigue resistance allows forged alloy round bars to perform reliably under harsh mechanical conditions, ensuring a longer lifespan for critical components.