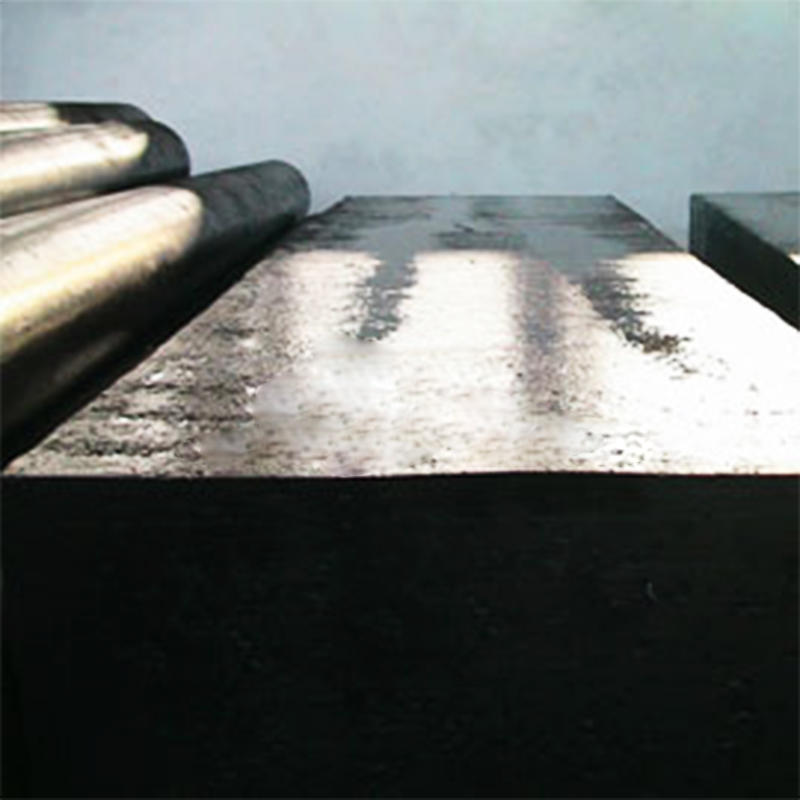
Insufficient Case Depth: Issue: Insufficient case depth occurs when the nitriding process does not achieve the desired depth of nitrogen diffusion into the alloy steel. This results in inadequate surface hardness and wear resistance, compromising the performance of the component. Prevention: To prevent insufficient case depth, carefully calibrate the nitriding process parameters, including temperature, time, and nitrogen potential. Ensure the steel's surface is properly prepared to remove any oxides or contaminants that may hinder nitrogen absorption. Conduct regular measurements of case depth to verify that the desired specifications are being met.
Over-Nitriding: Issue: Over-nitriding leads to the formation of excessively hard and brittle surface layers, which can result in stress-induced cracking or premature failure of the component under operational loads. Prevention: Avoid over-nitriding by adhering strictly to the recommended time and temperature limits specified for the nitriding process. Monitor the nitriding environment continuously to ensure that nitrogen levels do not exceed optimal ranges. Implement real-time process controls to prevent deviations that could lead to over-nitriding.
Surface Cracking: Issue: Surface cracking can occur due to excessive nitriding, rapid temperature changes, or improper handling of the steel. These cracks can undermine the integrity and functionality of the component. Prevention: Minimize the risk of surface cracking by controlling the heating and cooling rates to avoid thermal shock. Use gradual temperature ramps and ensure uniform heating throughout the nitriding process. Inspect the steel for any pre-existing cracks or defects before initiating nitriding, and employ appropriate handling procedures to prevent mechanical damage.
Poor Adhesion of Nitrided Layer: Issue: Poor adhesion of the nitrided layer can result in delamination or flaking, reducing the effectiveness of the nitriding treatment and potentially leading to failure of the component. Prevention: Ensure thorough cleaning and degreasing of the alloy steel to remove contaminants that could affect adhesion. Maintain optimal nitriding parameters and monitor the bonding strength between the nitrided layer and the base material. Perform adhesion tests to confirm that the nitrided layer adheres properly and meets performance criteria.
Non-uniform Nitriding: Issue: Non-uniform nitriding can lead to uneven distribution of the nitrided layer, resulting in inconsistent hardness and performance characteristics across the steel surface. Prevention: Ensure uniform exposure of all surfaces to the nitriding environment by properly positioning and loading components within the nitriding chamber. Maintain consistent process conditions, including temperature and gas flow, and regularly inspect for uniformity in nitriding results. Implement rigorous process controls to detect and correct any deviations from uniformity.
Inconsistent Hardness: Issue: Variability in hardness across the nitrided surface can result in uneven performance and may compromise the reliability of the component. Prevention: Regularly calibrate nitriding equipment and ensure that process conditions remain stable throughout the treatment. Perform periodic hardness testing to verify consistency and make adjustments as needed. Implement quality control measures to detect and address any deviations in hardness.
Cratering: Issue: Cratering refers to the formation of crater-like defects on the surface of the alloy steel, which can be caused by uneven nitriding or contamination within the nitriding chamber. Prevention: Ensure that the steel is thoroughly cleaned and degreased prior to nitriding to remove any contaminants. Regularly inspect and maintain the nitriding equipment to prevent contamination. Monitor and control the nitriding atmosphere to ensure uniform gas distribution and avoid localized defects.
Hot processed alloy steel square bar