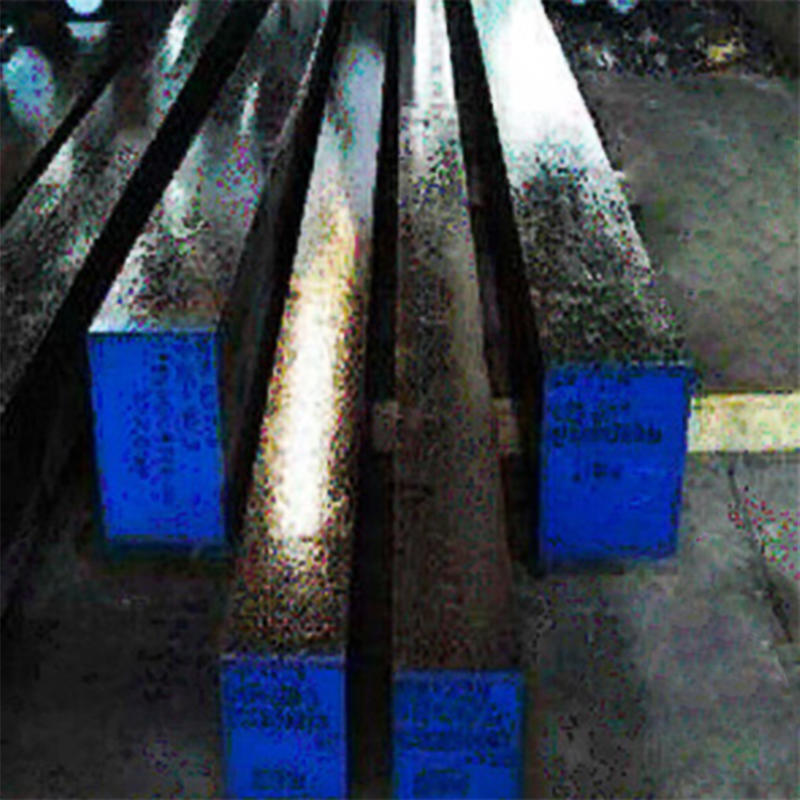
The surface finish of alloy steel changes significantly after nitriding due to the formation of a hard, wear-resistant layer on the surface. Here are the key changes and characteristics of the surface finish post-nitriding:
Improved Wear Resistance: The formation of a hard nitrided layer on the steel surface greatly enhances its wear resistance. This layer acts as a protective barrier against mechanical wear, reducing the material loss during frictional contact. The nitrided layer's enhanced wear resistance is particularly beneficial for components in high-wear environments, such as bearings, valve parts, and extrusion screws. The nitrided surface reduces the frequency of maintenance and replacement, leading to lower operational costs and improved efficiency in machinery.
Surface Roughness: Nitriding can cause a slight increase in surface roughness due to the formation of nitrides. The initial surface finish of the alloy steel plays a significant role in determining the final roughness post-nitriding. Finely machined or polished surfaces tend to maintain a smoother finish, while rougher surfaces may experience a more noticeable increase in roughness. This change in roughness can be minimized by controlling the nitriding process parameters and using post-nitriding finishing techniques, such as polishing or grinding, to achieve the desired surface texture. Maintaining a smooth surface finish is crucial for applications where low friction and high precision are required.
Color Change: The surface of nitrided alloy steel typically exhibits a color change, ranging from dark grey to black. This color change results from the formation of iron nitrides on the surface. The darkened surface is a visual indicator of a successful nitriding process and can also provide some degree of corrosion resistance. The uniform color change enhances the aesthetic appeal of the component and serves as a quality control marker for consistent nitriding treatment across batches.
Surface Structure: Nitriding creates a complex surface structure characterized by the formation of a compound layer, also known as the white layer, on the top surface. This compound layer consists of iron nitrides, primarily ε-Fe2-3N and γ'-Fe4N, which contribute to the increased hardness and wear resistance. Beneath the compound layer lies the diffusion zone, where nitrogen atoms have penetrated the steel matrix, enhancing its mechanical properties. The compound layer is typically very thin (a few micrometers) but plays a critical role in protecting the underlying material from wear and fatigue. This structured layering enhances the overall performance and longevity of the component.
Corrosion Resistance: The nitriding process can enhance the corrosion resistance of alloy steel by forming a protective layer of nitrides on the surface. These nitrides act as a barrier, preventing the ingress of corrosive agents and reducing the rate of oxidation and rust formation. This improvement in corrosion resistance is particularly beneficial for components exposed to harsh environments, such as chemical processing equipment, marine applications, and automotive parts. The enhanced corrosion resistance extends the service life of the components and reduces the need for frequent maintenance or protective coatings.
Surface Integrity: Nitriding improves the overall surface integrity of alloy steel by inducing compressive residual stresses in the surface layer. These compressive stresses counteract tensile stresses that can lead to crack initiation and propagation, thereby enhancing the fatigue resistance of the component. Improved surface integrity ensures that nitrided components can withstand cyclic loading and extend their operational lifespan in demanding applications. The nitrided layer also provides better resistance to impact and thermal cycling, making it suitable for dynamic and high-temperature environments.