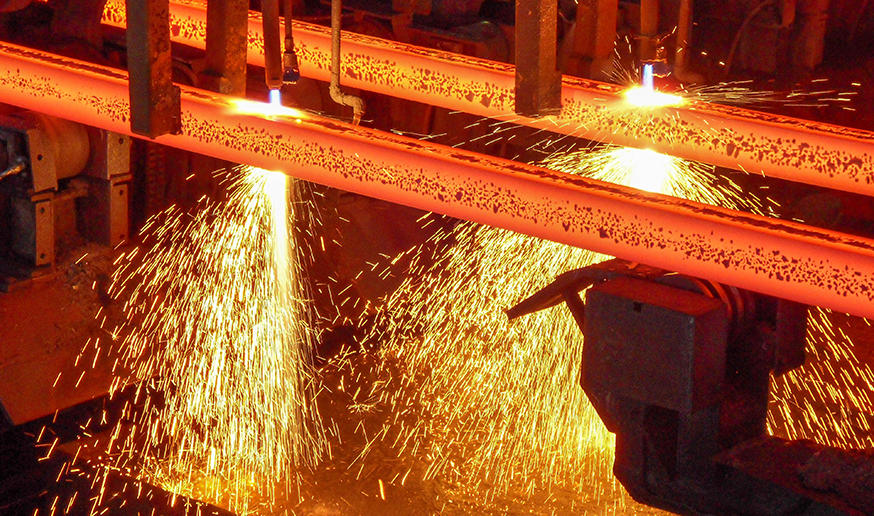
The machinability of forged alloy round bars can vary depending on the specific alloy composition and heat treatment. Forged alloy round bars can have different machinability characteristics compared to other materials like stainless steel or carbon steel. Here are some factors to consider:
The machinability of forged alloy round bars is profoundly influenced by the alloy composition. Alloying elements like chromium, molybdenum, and nickel can significantly impact machinability. For instance, chromium improves corrosion resistance and hardenability but may increase tool wear if present in high concentrations. Molybdenum enhances strength and hardenability, promoting chip breaking and reducing tool wear during machining. Nickel improves toughness and resistance to corrosion but can contribute to work hardening and challenges in chip formation. Conversely, elements like titanium or vanadium may improve strength and wear resistance but can pose challenges due to their tendency to work-harden during machining, requiring specialized tooling and strategies.
Forged alloy round bars typically exhibit high hardness and a refined microstructure due to the forging process. While high hardness enhances mechanical properties such as strength and wear resistance, it can also pose challenges during machining. The hardness of the material influences chip formation, tool wear, and surface finish. The microstructure, which is influenced by factors like forging temperature and cooling rate, affects machinability by influencing the distribution of alloying elements and phases within the material.
The heat treatment regimen employed during manufacturing significantly affects the machinability of forged alloy round bars. Heat treatments such as annealing, quenching, and tempering are utilized to optimize mechanical properties while balancing machinability. Annealing softens the material, reducing hardness and internal stresses, thereby improving machinability. Conversely, improper heat treatment can result in undesirable microstructural changes, such as retained austenite or carbide precipitation, leading to increased tool wear and surface roughness during machining.
Effective chip control is essential for maintaining process stability and surface finish in machining operations. Proper chip control strategies, such as employing chip breakers, controlling chip thickness, and optimizing coolant delivery, are crucial for preventing chip-related issues like built-up edge formation, poor surface finish, and tool breakage. Selecting the appropriate cutting tool geometry, rake angle, and cutting fluid can help optimize chip formation and evacuation, improving machinability and productivity.
Ensuring the stability of the workpiece is critical for achieving dimensional accuracy, surface finish, and tool life in machining operations. Rigorous fixturing, clamping, and support systems are employed to minimize workpiece deflection, vibration, and chatter during machining. Damping techniques, such as vibration absorbers and tuned mass dampers, may be utilized to reduce resonance and enhance machining stability, particularly when dealing with large-diameter round bars or thin-walled components.
Effective lubrication and coolant management are essential for reducing friction, dissipating heat, and prolonging tool life during machining. Proper selection and application of cutting fluids, lubricants, and coolant systems help minimize heat generation, tool wear, and surface roughness while improving chip evacuation and surface finish. Advanced coolant technologies, such as high-pressure coolant delivery systems and minimum quantity lubrication (MQL), offer enhanced cooling and lubrication capabilities, further improving machinability and productivity.