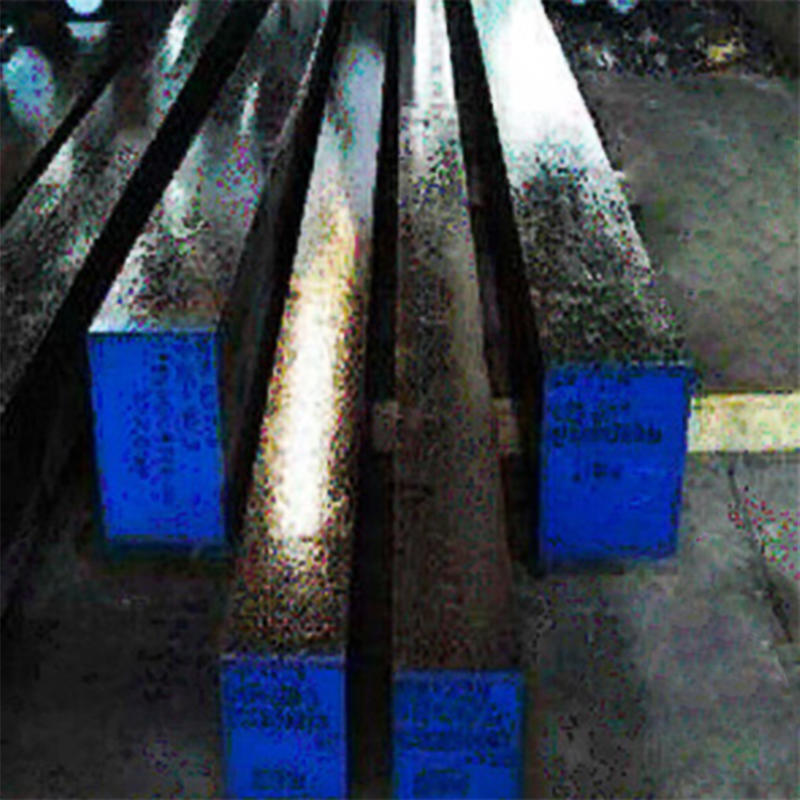
Enhanced Hardness and Wear Resistance: Nitriding significantly improves the surface hardness of alloy steel through a process in which nitrogen is diffused into the steel's surface. This treatment results in the formation of a hard, nitride-rich surface layer. The hardness of this layer can reach values significantly higher than those of untreated steel, with typical hardness values often exceeding 60 HRC (Rockwell Hardness C scale). In high-temperature applications, where surfaces are exposed to intense wear and abrasive forces, the nitrided surface layer helps maintain critical dimensions and functionality. This enhancement in wear resistance is crucial for extending the operational life of components, reducing the frequency of maintenance or replacement, and improving overall system reliability.
Thermal Stability: The nitriding process imparts a high degree of thermal stability to alloy steel. The nitride layer formed during nitriding is chemically stable and retains its hardness at elevated temperatures, often up to 500°C to 600°C (932°F to 1112°F), depending on the alloy and nitriding conditions. This stability is achieved through the formation of a dense, stable nitride layer that resists thermal softening and degradation. As a result, components made from nitrided steel can operate reliably in high-temperature environments without experiencing significant loss of mechanical properties, such as hardness or tensile strength.
Oxidation Resistance: The nitrided surface of alloy steel provides enhanced resistance to oxidation and high-temperature corrosion. The presence of nitrides within the surface layer acts as a protective barrier against oxidative processes. This barrier helps prevent the formation of oxide scales that can lead to material degradation and failure. In high-temperature applications, where the risk of oxidation is elevated due to exposure to oxygen and elevated temperatures, nitrided steel maintains its integrity and operational performance, thereby reducing the likelihood of premature component failure and extending the service life of the parts.
Reduced Thermal Expansion: One of the significant benefits of nitriding is its effect on the thermal expansion properties of alloy steel. The nitrided layer effectively lowers the coefficient of thermal expansion of the steel, meaning that it undergoes less dimensional change in response to temperature fluctuations. This reduction in thermal expansion is particularly important in precision applications where dimensional stability is critical. Components made from nitrided steel will exhibit less warping or distortion due to temperature variations, ensuring that they maintain their precise tolerances and fit within assemblies even under varying thermal conditions.
Improved Fatigue Resistance: Nitriding alloy steel enhances fatigue resistance by introducing compressive residual stresses in the surface layer. These compressive stresses counteract the tensile stresses that occur during cyclic loading, thereby reducing the likelihood of fatigue crack initiation and propagation. In high-temperature applications where components are subjected to repeated or cyclic loads, this improvement in fatigue resistance is crucial. It helps to prevent premature failure due to fatigue, ensuring that components can withstand prolonged use under demanding conditions without succumbing to fatigue-related issues.
Lower Friction and Lubrication Requirements: The nitriding process results in a smooth, hard surface that significantly reduces friction between mating components. This reduction in friction is beneficial in high-temperature environments where lubrication can break down or be less effective. The reduced friction provided by the nitrided layer decreases the wear rate of components, improves operational efficiency, and minimizes the need for frequent lubrication. This characteristic is especially valuable in systems where maintaining effective lubrication is challenging due to high temperatures or aggressive operating conditions.