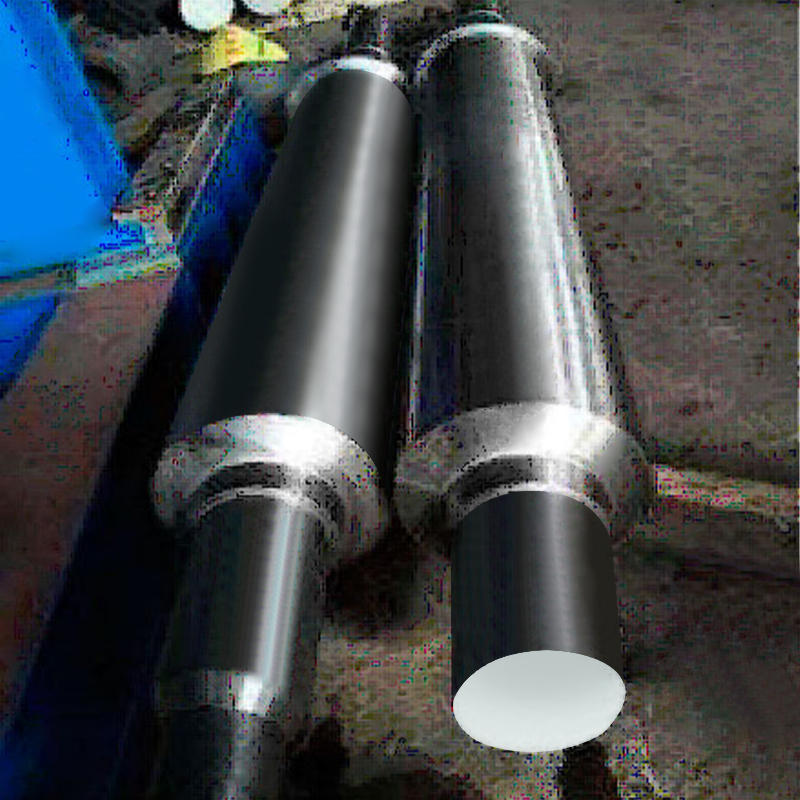
Forged step shafts excel in the transfer of rotational force (torque) between various mechanical components, such as gears, pulleys, and bearings, in a system. The stepped design of these shafts is integral in accommodating components of different sizes. By using multiple stepped sections, each one can fit perfectly with its corresponding component, ensuring a seamless energy transfer. This helps reduce torque loss, which directly impacts the system's operational efficiency. For high-torque applications, forged step shafts provide better performance than shafts with a uniform diameter, as they help minimize energy dissipation through slippage or inefficient coupling.
Forging a step shaft involves compressing the material under extreme pressure, aligning the metal grains and creating a denser structure, which vastly improves the material's strength. The enhanced grain structure achieved through forging makes these shafts exceptionally resistant to high stresses. This characteristic is particularly beneficial in heavy-duty applications where shafts are subjected to frequent, repeated stresses. Unlike cast or machined shafts, which may experience weaknesses from air pockets or inconsistencies, forged step shafts are nearly impervious to cracking and wear under demanding conditions. The material’s resistance to deformation ensures that these shafts maintain their functional integrity over long operational cycles, offering improved reliability and reducing the frequency of part replacements, thus minimizing downtime and associated costs.
One of the primary benefits of forged step shafts is their ability to efficiently distribute the operational load across multiple surfaces. In typical shaft systems, point loading (where stress is concentrated at a specific spot) can lead to material fatigue, failure, and excessive wear. The stepped design, however, helps spread the load evenly along the shaft. Each step can be designed with specific dimensions that correspond to the required load-bearing capacity, which optimizes the system's overall stress management. The result is less strain on individual components, less wear on bearings or gears, and longer operational life for all connected parts. The ability to distribute forces evenly ensures smoother operations, less vibration, and lower friction between moving parts, which leads to higher efficiency.
Vibration and noise are common issues in mechanical systems, particularly in rotating machinery. Excessive vibration can cause undue stress on components, accelerating wear, reducing efficiency, and even leading to catastrophic failures. Forged step shafts, with their precise tolerances and balanced design, contribute significantly to minimizing vibration. Their solid, uniform structure and accurate manufacturing help eliminate imbalances that could otherwise lead to oscillations and noise. As a result, the system operates with smoother rotations, which leads to less energy loss due to friction and a quieter working environment.
The tight tolerances and high precision that come with the forging process enable forged step shafts to fit seamlessly with other system components. Precision in alignment is crucial for ensuring that the shaft works optimally within the system, with minimal friction and wear. Misalignment, even by a small amount, can lead to inefficient power transmission, causing slippage or increased friction, which wastes energy. With forged step shafts, the perfect fit ensures that the system operates with minimal resistance, thus improving energy efficiency. Components that are perfectly aligned will wear evenly, reducing the need for premature repairs or replacements, thereby extending the life of the entire system.