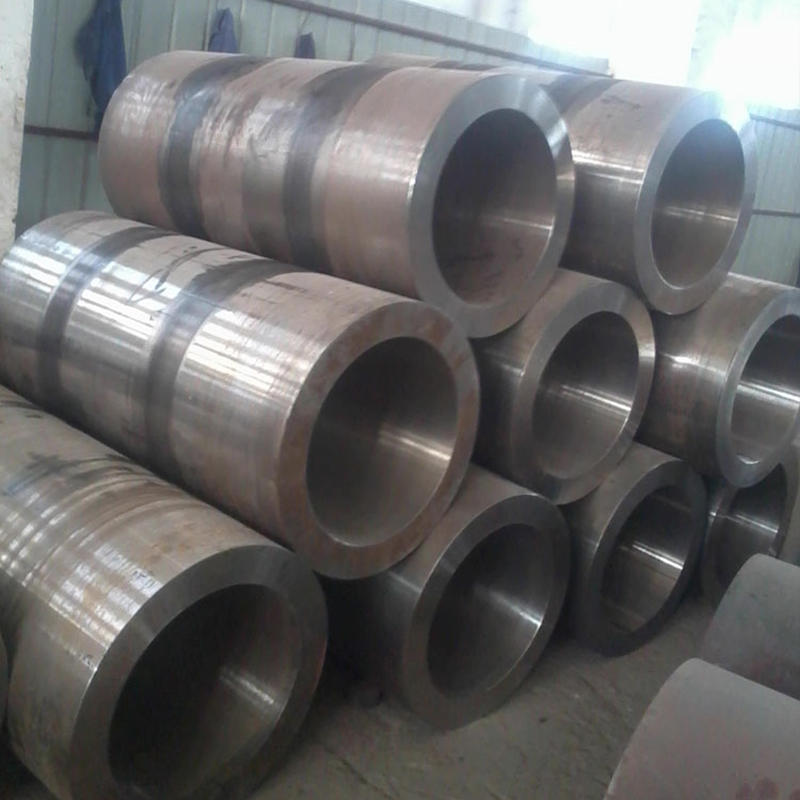
Proper Sizing and Selection: Accurate sizing and selection of a hydraulic cylinder are fundamental to achieving energy efficiency. A high-pressure hydraulic cylinder that is appropriately matched to the specific application will operate more efficiently, ensuring the required load is moved with minimal energy input. Over-sizing the cylinder leads to unnecessary power consumption, as it might require more energy to generate the force needed for a relatively lighter load. Conversely, an undersized cylinder will struggle to meet performance requirements, potentially overloading the system and causing inefficiency. Therefore, careful analysis of the required pressure, force, and stroke length is necessary for selecting a cylinder that operates with maximum efficiency and minimal energy waste.
Use of Variable Displacement Pumps: Integrating variable displacement pumps with high-pressure hydraulic cylinders provides a significant boost to energy efficiency. Unlike fixed displacement pumps that deliver a constant flow regardless of system demand, variable displacement pumps can adjust their flow output based on the load requirements. This means that energy is only used as needed, reducing the power consumed when the demand is lower. In applications where the load varies, this adaptation can result in considerable energy savings. Variable displacement pumps can reduce wear on system components by ensuring smoother operation, contributing to both energy efficiency and prolonged equipment lifespan.
Optimized Hydraulic Fluid Selection: The choice of hydraulic fluid is crucial in determining the efficiency of the hydraulic system. Fluids with lower viscosity create less resistance as they flow through the system, allowing for smoother operation and reducing the energy required to move the fluid through pipes and valves. Using fluids with high thermal stability ensures that the system maintains optimal performance across a range of operating temperatures, preventing energy losses due to overheating or excessive cooling needs. Employing biodegradable and environmentally friendly fluids helps mitigate the environmental impact of the hydraulic system, aligning with energy efficiency goals and sustainability efforts.
Improved Seal Technology: The sealing system within a high-pressure hydraulic cylinder plays a significant role in energy efficiency. Poorly designed or worn seals can result in hydraulic fluid leakage, which compromises system pressure and causes inefficiencies. Modern sealing materials such as polyurethane, PTFE (polytetrafluoroethylene), and other advanced polymers provide excellent wear resistance and low friction, which reduces energy losses due to leakage and friction between the piston and cylinder walls. These seals help maintain consistent pressure, contributing to optimal energy usage. By selecting the most advanced sealing technology and regularly maintaining seals, companies can minimize energy losses and extend the lifespan of the hydraulic cylinder.
Energy Recovery Systems: Energy recovery systems, such as hydraulic accumulators, are key to enhancing energy efficiency in high-pressure hydraulic systems. These systems capture excess energy that would otherwise be lost, particularly during cycles when energy demand decreases. For example, during a retract stroke, an accumulator can store the hydraulic energy and then release it during the extension stroke, reducing the need for additional energy input from the pump. By integrating energy recovery systems into the design, hydraulic systems can operate more efficiently, saving on energy costs and reducing the load on the pump, thus prolonging the lifespan of the entire system.