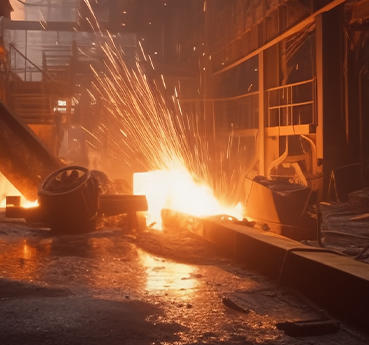
Forging is a processing method that utilizes forging machinery to apply pressure to metal billets, causing them to undergo plastic deformation to obtain forgings with certain mechanical properties, shapes, and sizes. It is one of the two major components of forging (forging and stamping). Forging can eliminate defects such as casting porosity in the smelting process of metals, optimize the microstructure, and, due to the preservation of complete metal flow lines, the mechanical properties of forgings are generally better than those of castings of the same material. Important parts in related machinery with high loads and severe working conditions, except for simple shapes that can be rolled into plates, profiles, or welded parts, are mostly made of forgings.
The deformation temperature of forging materials
The starting recrystallization temperature of steel is divided by 800 ℃, with hot forging occurring above 800 ℃; Forging between 300 and 800 ℃ is called warm forging or semi-hot forging, and forging at room temperature is called cold forging. Forgings used in most industries are hot forging, while warm and cold forging is mainly used for forging parts such as automobiles and general machinery. Warm and cold forging can effectively save materials.
The category of forging
According to the forging temperature, it can be divided into hot forging, warm forging, and cold forging.
According to the forming mechanism, forging can be divided into free forging, die forging, ring rolling, and special forging.
1. Free forging. The processing method of forging refers to the use of simple universal tools or the direct application of external forces between the upper and lower anvils of forging equipment to deform the billet and obtain the required geometric shape and internal quality. Forgings produced using the free forging method are called free forgings. Free forging mainly produces small batches of forgings, using forging equipment such as hammers and hydraulic presses to shape and process the blanks and obtain qualified forgings. The basic processes of free forging include upsetting, elongation, punching, cutting, bending, twisting, displacement, and forging. Free forging adopts the hot forging method.
2. Die forging. Die forging can be divided into open-die forging and closed-die forging. Metal billets are formed by compression deformation in the forging die chamber with a certain shape to obtain forgings. Die forging is generally used to produce parts with small weights and large batch sizes.
Die forging can be divided into hot die forging, warm forging, and cold forging. Warm forging and cold forging are the future development directions of die forging and also represent the level of forging technology. According to material classification, die forging can also be divided into black metal die forging, non-ferrous metal die forging, and powder product forming. As the name suggests, the materials are black metals such as carbon steel, non-ferrous metals such as copper and aluminum, and powder metallurgy materials. Extrusion should belong to die forging and can be divided into heavy metal extrusion and light metal extrusion. It should be noted that the billet cannot be completely restricted. Therefore, it is necessary to strictly control the volume of the billet, control the relative position of the forging die, and measure the forgings, striving to reduce the wear of the forging die.
3. Grinding ring. Ring rolling refers to the production of circular parts with different diameters using specialized equipment such as ring rolling machines, and is also used to produce wheel-shaped parts such as car wheels and train wheels.
4. Special forging. Special forging includes forging methods such as roll forging, cross wedge rolling, radial forging, and liquid die forging, all of which are more suitable for producing certain specially shaped parts.
For example, roll forging can serve as an effective preforming process, significantly reducing the subsequent forming pressure; Cross wedge rolling can produce parts such as steel balls and transmission shafts; Radial forging can produce large forgings such as gun barrels and step shafts.
forging die
According to the movement mode of the forging die, forging can be divided into swing forging, swing rotary forging, roll forging, cross wedge rolling, ring rolling, and oblique rolling. Rotary forging, rotary forging, and precision forging can also be used for the 400MN (40000 ton) heavy-duty aviation forging hydraulic press ring in China. To improve the utilization rate of materials, roll forging and cross-rolling can be used as the preceding processes for processing slender materials. Rotary forging, like free forging, is also locally formed, and its advantage is that it can be formed even under smaller forging forces compared to the size of the forging. This forging method, including free forging, involves the expansion of materials from the vicinity of the mold surface to the free surface during processing, making it difficult to ensure accuracy. Therefore, by controlling the movement direction of the forging die and the rotary forging process with a computer, complex-shaped and high-precision products can be obtained with lower forging force, such as producing forgings with multiple varieties and large sizes of steam turbine blades.
The mold movement and degrees of freedom of forging equipment are inconsistent. According to the characteristics of deformation limitations at the bottom dead center, forging equipment can be divided into the following four forms:
1. Limited forging force form: a hydraulic press that directly drives the slider with oil pressure.
2. Quasi-stroke limit method: a hydraulic press that drives the crank connecting rod mechanism by hydraulic pressure.
3. Stroke limitation method: a mechanical press with a crank, connecting rod, and wedge mechanism driving the slider.
4. Energy limitation method: Utilize the spiral mechanism of the screw and friction press. To achieve high accuracy during hot testing of heavy-duty aviation forging hydraulic presses, attention should be paid to preventing overload at the bottom dead center, controlling speed and mold position. Because these will have an impact on the tolerance, shape accuracy, and life of forgings. In addition, to maintain accuracy, attention should also be paid to adjusting the clearance between the slider guide rails, ensuring stiffness, adjusting the lower dead center, and utilizing auxiliary transmission devices.
Forged slider
Forging sliders can be divided into vertical and horizontal movements (used for forging slender parts, lubrication, cooling, and forging high-speed production parts), and compensation devices can be used to increase movement in other directions. The above methods are different, and the forging force, process, material utilization rate, output, dimensional tolerance, and lubrication and cooling method required to successfully forge the large disc-type product are all different. These factors are also factors that affect the level of automation.Materials used for forging
The main materials used for forging are carbon steel and alloy steel with various compositions, followed by aluminum, magnesium, copper, titanium, and their alloys. The original state of materials includes bars, ingots, metal powders, and liquid metals. The ratio of the cross-sectional area of a metal before deformation to the cross-sectional area after deformation is called the forging ratio. The correct selection of forging ratio, reasonable heating temperature and insulation time, reasonable initial and final forging temperatures, reasonable deformation amount, and deformation speed are closely related to improving product quality and reducing costs. Generally, small and medium-sized forgings use round or square bars as billets. The grain structure and mechanical properties of the bar material are uniform and good, with accurate shape and size, good surface quality, and easy-to-organize mass production. As long as the heating temperature and deformation conditions are reasonably controlled, high-performance forgings can be forged without significant forging deformation. Ingots are only used for large forgings. The ingot is an as-cast structure with large columnar crystals and a loose center. Therefore, it is necessary to break the columnar crystals into fine grains through large plastic deformation and compact them loosely to obtain metal structure and mechanical properties. Powder metallurgy preforms made by pressing and firing can be forged into powder forgings without burrs in the hot state. The density of forging powder is close to that of general die forgings, with good mechanical properties and high accuracy, which can reduce subsequent cutting processing. The internal structure of powder forgings is uniform without segregation and can be used to manufacture small gears and other workpieces. However, the price of powder is much higher than that of ordinary bars, and its application in production is subject to certain limitations. Applying static pressure to the liquid metal poured into the mold cavity, which solidifies, crystallizes, flows, undergoes plastic deformation, and forms under pressure, can obtain the required shape and performance of the die forging. Liquid metal forging is a forming method that lies between die casting and forging, especially suitable for complex thin-walled parts that are difficult to form in general forging. In addition to common materials such as carbon steel and alloy steel with various compositions, followed by aluminum, magnesium, copper, titanium, and their alloys, the deformation alloys of iron-based high-temperature alloys, nickel-based high-temperature alloys, and cobalt-based high-temperature alloys are also completed by forging or rolling. However, these alloys have relatively narrow plastic zones, so the difficulty of forging is relatively high. Different materials have strict requirements for heating temperature, opening forging temperature, and final forging temperature.
Forging process flow
Different forging methods have different processes, among which the hot die forging process is the longest, and the general order is: forging blank cutting; Forging billet heating; Roll forging blank preparation; Die forging forming; Cutting edges; Punching; Correction; Intermediate inspection, checking the dimensions and surface defects of forgings; Heat treatment of forgings to eliminate forging stress and improve metal cutting performance; Cleaning, mainly to remove surface oxide scale; Correction; Inspection: Generally, forgings need to undergo appearance and hardness inspection, while important forgings also need to undergo chemical composition analysis, mechanical properties, residual stress testing, and non-destructive testing.
Characteristics of Forgings
Compared with castings, metal can improve its microstructure and mechanical properties after forging processing. After hot working and deformation by the forging method, the casting structure transforms from coarse dendrites and columnar grains to equiaxed recrystallized structures with finer and uniform sizes due to the deformation and recrystallization of the metal. This causes the original segregation, porosity, porosity, slag inclusion, and other compaction and welding in the steel ingot, making the structure more compact and improving the plasticity and mechanical properties of the metal. The mechanical properties of castings are lower than those of forgings of the same material. In addition, forging processing can ensure the continuity of the metal fiber structure, keeping the fiber structure of the forging consistent with the shape of the forging. The metal flow line is complete, which can ensure that the parts have good mechanical properties and long service life. Forgings produced by precision forging, cold extrusion, warm extrusion, and other processes are incomparable to castings. Forgings are objects that are shaped by plastic deformation to meet the required shape or suitable compression force when metal is subjected to pressure. This power is typically achieved through the use of a hammer or pressure. The forging process builds exquisite particle structures and improves the physical properties of the metal. In the practical use of components, a correct design can ensure that the particle flow is in the direction of the main pressure. Castings are metal-formed objects obtained through various casting methods, that is, molten liquid metal is injected into pre-prepared molds through pouring, injection, suction, or other casting methods, cooled, and then subjected to sand removal, cleaning, and post-treatment to obtain objects with a certain shape, size, and performance.
Analysis of forging level
The Chinese forging industry has developed on the basis of introducing, digesting, and absorbing foreign technology. After years of technological development and transformation, the technical level of enterprises in the industry has greatly improved, including process design, forging technology, heat treatment technology, machining technology, product testing, and other aspects.
(1) Advanced manufacturers in process design generally adopt hot processing computer simulation technology, computer-aided process design, and virtual technology, improving the level of process design and product manufacturing capabilities. Introduce and apply simulation programs such as DATAFOR, GEMARC/AUTOFORGE, DEFORM, LARSTRAN/SHAPE, and THERMOCAL to achieve process control of computer design and thermal processing.
(2) Most hydraulic presses with forging technology of 40MN and above are equipped with 100-400t. m main forging operators and 20-40t. m auxiliary operators. A considerable number of operators use computer control to achieve comprehensive control of the forging process, allowing forging accuracy to be controlled within ± 3mm. Online measurement of forgings uses laser size measurement devices.
(3) The focus of heat treatment technology is to improve product quality, enhance heat treatment efficiency, save energy, and protect the environment. If the heating process of the heating furnace and heat treatment furnace is controlled by a computer, the burner can be controlled to achieve automatic adjustment of combustion, furnace temperature, automatic ignition, and heating parameter management; Waste heat utilization, heat treatment furnaces equipped with regenerative combustion chambers, etc; By using polymer quenching oil tanks with low pollution capacity and effective cooling control, various water-based quenching media are gradually replacing traditional quenching oil.
(4) The proportion of CNC machine tools in the machining technology industry is gradually increasing. Some enterprises in the industry have machining centers and are equipped with proprietary machining machinery according to different types of products, such as five-coordinate machining centers, blade machining machines, roller mills, roller lathes, etc.
(5) Quality assurance measures: Some domestic enterprises have equipped themselves with the latest detection instruments and testing technologies, modern automated ultrasonic testing systems with computer-controlled data processing, and various specialized automatic ultrasonic testing systems to complete certification of various quality systems. The key production technology of high-speed heavy-duty gear forgings has been continuously overcome, and on this basis, industrial production has been achieved. Based on introducing advanced production technology and key equipment from abroad, China has been able to design and manufacture production equipment for high-speed and heavy-duty gear forgings on its own. These equipment have approached the international advanced level, and the improvement of technology and equipment level has effectively promoted the development of the domestic forging industry.
The importance of forging
Forging production is one of the main processing methods for providing mechanical parts blanks in the mechanical manufacturing industry. By forging, not only can the shape of mechanical parts be obtained, but also the internal structure of the metal can be improved, and the mechanical and physical properties of the metal can be enhanced. Generally, important mechanical parts with high stress and requirements are manufactured using forging production methods. Important components such as turbine generator shafts, rotors, impellers, blades, retaining rings, large hydraulic press columns, high-pressure cylinders, steel rolling mill rolls, internal combustion engine crankshafts, connecting rods, gears, bearings, and artillery in the national defense industry are all produced through forging. [7] Therefore, forging production is widely used in industries such as metallurgy, mining, automobiles, tractors, harvesting machinery, petroleum, chemical industry, aviation, aerospace, weapons, etc. Even in daily life, forging production also plays an important role. In a sense, the annual output of forgings, the proportion of die forgings in the total output of forgings, as well as the size and ownership of forging equipment, reflect to a certain extent the industrial level of a country.